

电动汽车电机预计将受益于Trelleborg的热塑性复合材料转子套筒设计,该设计改进了材料和工艺,以生产轻质、节能的部件。
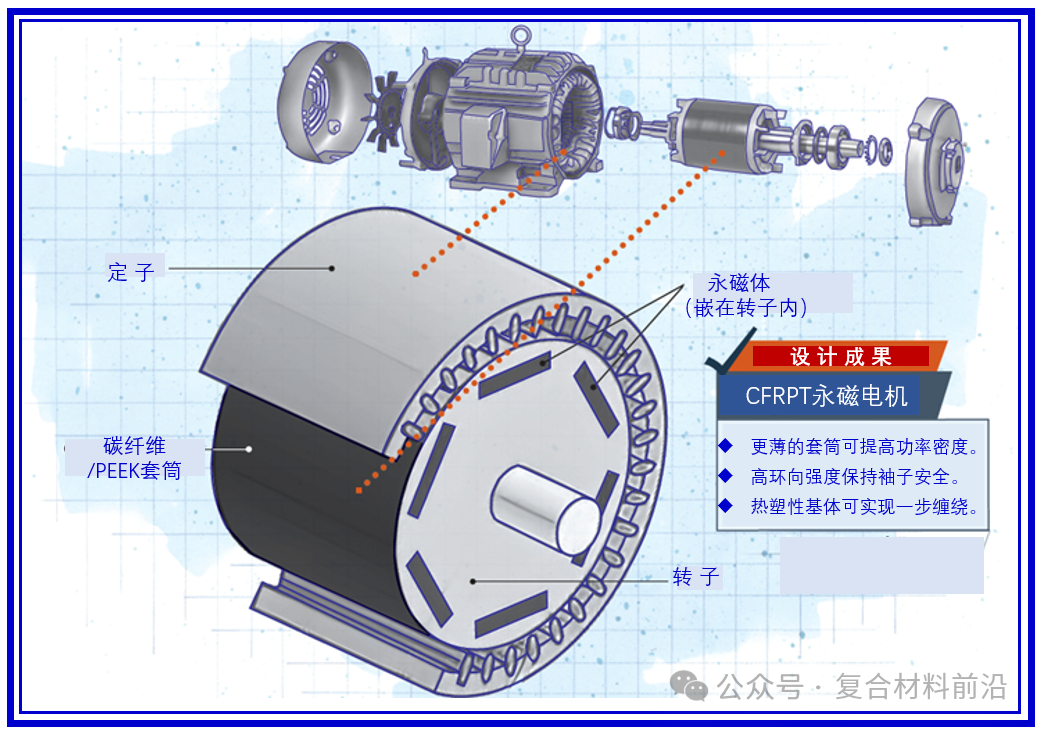
随着电动汽车(EV)技术的进步,以改善车辆的性能和范围,电池技术可能会抓住许多头条新闻,但同样重要的是电机,将电池能量转换为车辆推进。多年来,一种称为永磁电机(PMM- permanent magnet motor )的电动汽车电机包含了一个碳纤维增强热固性套管,该套管缠绕在PMM的转子上。套筒可防止转子组件在高转速下飞散。在最近的一项进步中,Trelleborg密封解决方案(美国纽约州奥尔巴尼市)利用热塑性树脂的一些优点,开发了一种改进的套筒设计。提高电机效率可能很快推动Trelleborg设计投入生产电动汽车电机。
在电动汽车市场,PMM最近已被选择用于几种生产车辆,而不是更常见的感应电机。其中包括特斯拉3型和雪佛兰 Bolt 和Volt。感应电动机具有相对较低的成本和较高的可靠性,但永磁同步电机提供更高的功率密度和更轻的重量。永磁电机的价格是一个决定性的劣势,因为永磁体的成本很高,而永磁体通常由稀土金属制成。因此,提高这些电机效率的每一项进步都是为它们构建业务案例的关键。这就是为什么Trelleborg的用于PMM的碳纤维增强热塑性塑料(CFRTP)套管在电动汽车市场受到认真考虑的原因。
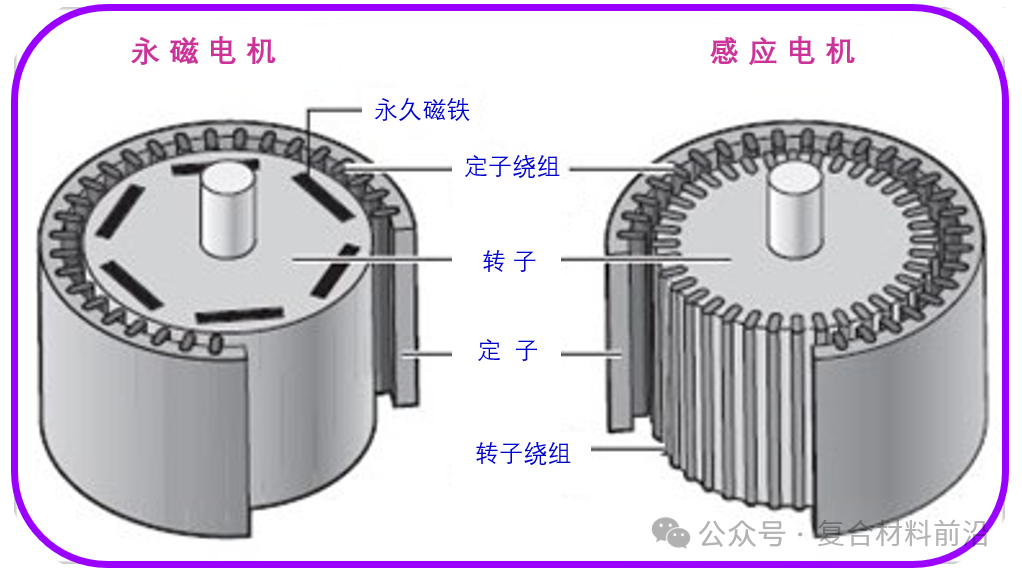
电动汽车电机选项。永磁电机通过嵌入磁铁产生自己的电磁场,这与感应电机不同,感应电机由电池的电能磁化
“我们已经建立了一对套筒在这个市场上的评估,虽然我们不能在这个时候详细说明,”特里堡产品经理,里德·希斯洛普报告。但电动汽车市场的商业应用似乎即将开始。Trelleborg成熟的复合材料设计和制造技术已被纳入PMMs,用于其他商业应用,如工业泵和机床驱动器、井下油气泵和HVAC设备。
为电动汽车供电
电动汽车电机通过电磁力运行。通过施加交流电,在静止部件定子中产生旋转磁场。定子包围旋转部件-转子-也磁化。由此产生的两个部件之间的磁吸引力和排斥力迫使转子旋转并为传动系统提供动力。
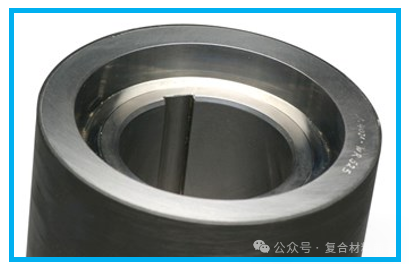
CFRTP套管。Trelleborg通过其自动纤维铺设(AFP)和原位固结,将碳纤维/热塑性复合材料直接缠绕到金属结构上。预拉伸复合材料使其即使在高转速应用(如永磁电机)中也能保持原位
在感应电动机中,导线(如铜或铝)缠绕或嵌入转子的叠层钢筒内,定子的交流电流感应转子的磁场。另一方面,永磁转子通过将永磁体包裹或粘结在转子上而产生自己的磁场。
PMM本质上比感应电机更高效,因为感应转子消耗电力来产生磁场,而PMM转子不消耗电力。PMM还提供高功率密度和扭矩密度:与感应电机相比,PMM可以通过更小、更轻的电机提供EV的目标功率和扭矩,从而支持更高性能和更大行驶范围的关键EV目标。PMMs还具有低噪声产生的特点,这对电动汽车市场具有吸引力。
效率设计
Trelleborg的热塑性复合材料套管由连续纤维增强预浸料制成,预浸料直接缠绕在PMM转子上。该公司的制造工艺,自动铺丝(AFP)与原位固结( ISC --in-situ consolidation),能够使套管适用于电动汽车PMM和几乎任何其他PMM应用。它们的尺寸范围从直径小于2.5厘米一直到为商用单通道类飞机推进设计的33厘米直径的原型电机转子套筒。
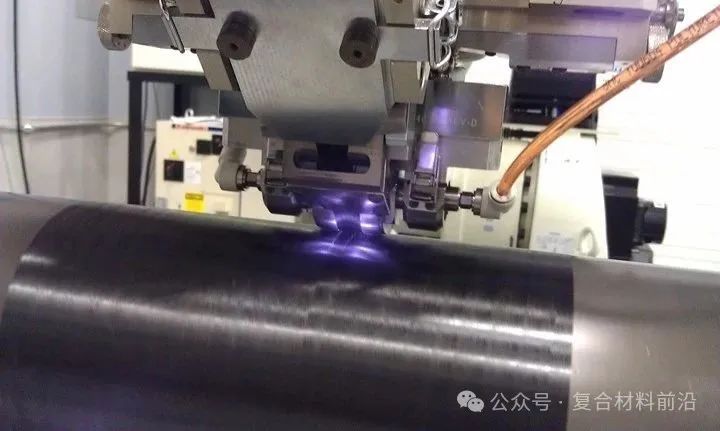
AFP/ISC用于设计。Trelleborg的制造工艺提供了新的设计自由度-例如,结构稳定的薄缠绕和厚缠绕,没有纤维波纹或屈曲。它还可以实现复合PMM套筒的一步制造
为了满足电动汽车应用的高性能要求,套筒由碳纤维增强聚醚醚酮(PEEK)预浸带制成。与其他材料和工艺相比,Trelleborg热塑性复合材料套管的材料和工艺创造了优越的设计自由度。碳纤维/聚醚醚酮套管的替代品包括上述热固性复合材料版本和钢版本。热塑性基体的特性,包括其优越的韧性和耐磨性、耐疲劳性和耐化学品性,使其非常适合电动汽车传动系统所经历的恶劣条件。
薄是Trelleborg设计和工艺的关键优势之一。转子套筒增加了转子磁体与定子之间的距离,该间隙越大,电机的电磁功率和效率越低。这意味着理想的套筒在尽可能薄的结构中提供高强度。Trelleborg的设计生产了一种套管,这种套管比热固性复合材料制成的套管更薄,单位厚度的套管比钢制成的套管更坚固。Trelleborg项目经理格雷厄姆·奥斯特兰德(Graham Ostrander)预计电动汽车电机的套筒厚度将为5到20层。
与钢相比,碳纤维增强复合材料的另一个重要性能特征是导电率低得多。低导电性可减少对磁场的干扰。薄型和低导电性的结合有助于碳纤维/聚醚醚酮套管最大化PMM的功率密度。
由于转子以非常高的速度旋转,套筒的设计也必须防止径向力引起疲劳或突然失效。构成永磁体的稀土金属是脆性的,因此在旋转过程中降低磁体上的应力对永磁电机的性能和耐久性至关重要。转子应用的绝大多数铺层为0°(环向角),以处理这些径向力,但也可根据需要加入轴向纤维(90°),以增加弯曲刚度。(Trelleborg的AFP机器能够以任何角度铺设3至25毫米宽的预浸带。)
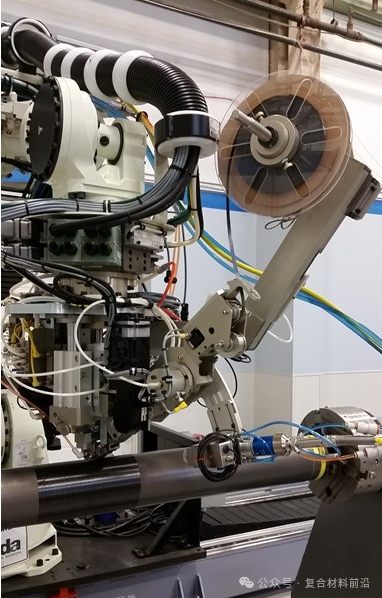
提高吞吐量。AFP/ISC技术可同时适应多个的过卷。与此处所示的一个长圆柱形部件不同,机器将转子端对端对齐,并编程为同时缠绕所有转子
承受径向力的关键是预拉伸复合材料-Trelleborg当前的AFP机器能够承受高达0.5公吨的张力(仅适用于连续纤维预浸料)。奥斯特兰德说:“这种预张力会产生一个作为压应力的环向应力,使复合材料套管在被过度缠绕的物品顶部保持原位。”。
“这种复合材料的高抗拉强度使得转子的旋转速度比任何粘合剂都要快,”他补充道。碳纤维的低热膨胀系数(CTE- coefficient of thermal expansion)也是套筒和转子之间强机械结合的因素,其重量轻,可处理快速加速和减速。
转子的期望转速和磁铁的重量共同决定所需的张力。奥斯特兰德报告说:“预拉伸缠绕纤维将套筒固定在转子上,温度范围很广,额定值为-40℃至80℃”。
设计成果:
更薄的套筒增加了功率密度。 高环向强度确保套筒稳固。 热塑性基质可实现一步过卷工艺。
设计制造
近年来,工程界经常追求“为制造而设计”—对产品的设计进行调整,以便更容易、更快和/或更具成本效益地制造产品。然而,在PMM套筒的情况下,可以将Trelleborg的过程描述为“以设计为导向的制造”,甚至“以制造为目的的设计”。也就是说,Trelleborg工程师开发了一种制造方法,减少了对产品设计的一些限制;而这种设计自由又使得制造流程更加高效。
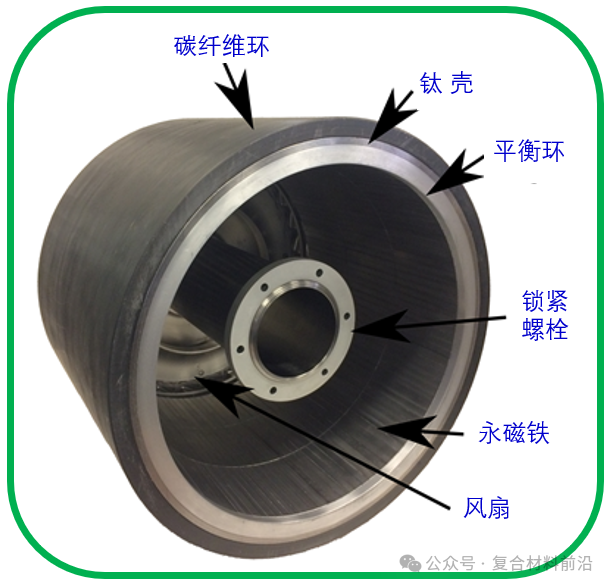
航空航天应用。随着Trelleborg继续与电动汽车制造商开展开发工作,该公司已帮助737级电动飞机进行概念验证研究。PMM转子,带有碳纤维/聚醚醚酮套管,由美国宇航局资助的伊利诺伊大学研究人员制造和测试。
Trelleborg的AFP可用于热固性或热塑性复合预浸料,但现场固结仅用于热塑性塑料。对于套筒应用,使用激光加热系统进行固结,与传统热气炬(HGT-hot gas torch)加热相比,该系统提高了该过程的速度和效率。
该工艺的一个重要特点是局部加热,加热时间短。高温会使转子退磁,使其无法使用。奥斯特兰德解释说:“尽管我们使用高热将聚合物熔化在一起,但加热的时间非常非常短。”。“我们的工艺不会使过度缠绕零件的净温度升高超过几摄氏度。”
热塑性复合套管的纤维直接缠绕在磁转子表面进行。奥斯特兰德强调:“我们有一种特殊的工艺,可以将复合材料放置在零件上,使其保持原位,而无需任何粘合剂或粘合到零件表面。”。沉积头加热正在铺设的材料和下面的基板(在本应用中,首先是转子表面,然后是先前放置的层),并在树脂熔融时施加压力。这使得聚合物链在引入的胶带和基板之间扩散,形成完整的粘合。
多次激光加热应用(最初在胶带铺设时进行,然后在AFP穿过该区域并随后铺层时重新加热)可使PEEK树脂完全结晶,从而使其在使用过程中的稳定性最大化。奥斯特兰德报告,对于碳纤维增强PEEK预浸料,压入材料压在基材上的压入点温度为450℃。PEEK在343℃下熔化,并且夹持温度通常设置为比熔体温度高60-120℃。“关键是保持低于聚合物的降解温度,”他说。
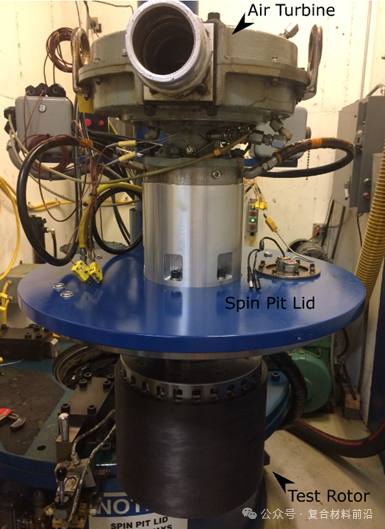
旋转试验。为了验证机械膨胀、转子动力学和旋转损失的分析模型,飞机转子原型在旋转坑内进行了试验(为了安全)。转子在以18000转/分的转速旋转时成功运行,比预期运行速度快20%。
原位固结热塑性复合材料使Trelleborg能够一步操作将PMM套筒缠绕在转子上。采用这种制造方法制造的结构不需要二次烘箱或热压罐固结,通常可获得约60%的纤维体积。奥斯特兰德说:“一旦零件完成了缠绕,就完成了最后的加工。”。
希斯洛普强调:“我们的工艺允许我们在一个操作中结合一系列不同的制造步骤。”。“这提高了整个制造过程的效率。”
相比之下,热固性复合材料套管需要一个多步骤的过程。热固性版本必须与转子分开制造,因为烤箱或热压罐固结会损坏磁铁。固化后,将这些套筒压在转子上或收缩配合在转子上。最后一步可防止热固性套管与热塑性套管一样薄。希斯洛普解释说:“由于不必在固化后将热塑性塑料套管压在转子上,因此不会产生会损坏薄套管的压缩载荷。”。
Trelleborg工艺已用于制造各种复合材料结构,其尺寸从内径0.5毫米到外径150厘米不等。它还制造了薄至两层、厚至7.5厘米、无纤维波纹或屈曲的稳定结构。奥斯特兰德说,在用其他固结方法制造的较厚层压板中,屈曲可能是一个问题。“当你把这些材料放在适当的地方,你最终会在层与层之间截留空气,但通过原位固结,空气在粘合过程中被挤出。”再加上热塑性预浸料几乎无限的挤出时间,奥斯特兰德总结道,“原位固结过程可以放大,使结构像飞机一样大。”
不确定的停机时间也使Trelleborg工艺能够缠绕非常长的零件。在转子套筒的情况下,这一能力意味着转子的长链可以设置在一条线上并同时缠绕。希斯洛普说:“这样,我们就提高了吞吐量,降低了客户的总体成本。”。
PMM的吸引力
稀土金属的成本仍然不利于PMM的总体拥有成本,这一事实以及地缘政治紧张(中国是稀土金属的主要供应商)可能会减缓PMM在EV系列车辆上的应用。但是,永磁同步电机的吸引力仍然很强,因为与感应电机相比,它具有更高的效率、扭矩和驱动范围。去年,路透社报道了主要汽车制造商为减少对稀土金属的依赖所做的大量努力。看来,大多数人是通过寻找替代材料的永久磁铁,而不是切换到感应电机。
无论是通过替代磁铁,还是通过更容易、成本更低的稀土金属供应,PMM似乎很可能被越来越多的电动汽车制造商采用。Trelleborg的热塑性复合材料套管等先进产品有望推动这一市场。

该资源面向电机和复合材料专家,讨论转子和定子套筒设计考虑因素、制造见解等。
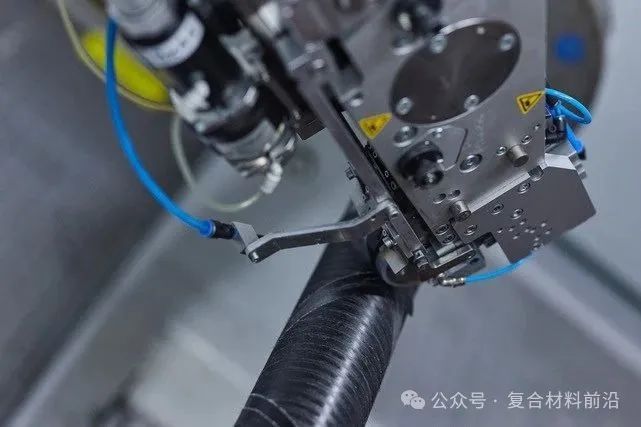
激光辅助卷绕(LATW)工艺
Alformet GmbH(Dörth,Germany)宣布发布白皮书,探讨热塑性复合材料(TPC- thermoplastic composite)转子和定子套管如何提高电机性能。
据该公司称,所有行业的电气化程度不断提高,对电动机的性能和生产提出了越来越高的要求。随着更高的转速、更严格的效率要求以及对具有挑战性的解决方案的推动,金属和热固性复合材料等传统材料显示出其局限性。然而,热塑性复合材料为优化电机设计提供了新的机遇。
TPC套管有哪些优点?
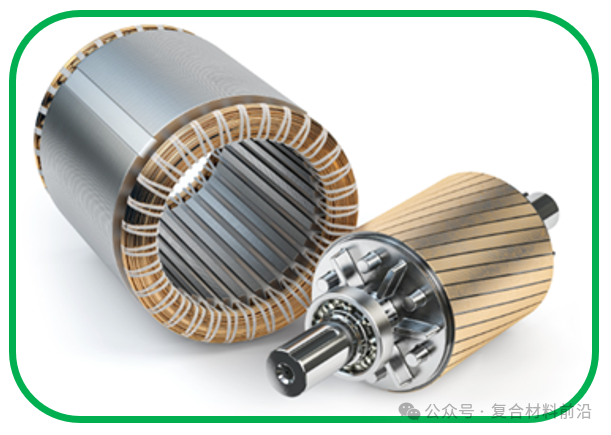
复合材料转子/定子套筒
阻尼和尺寸稳定性。TPC与碳纤维相结合,提供接近零的热膨胀和增强的振动阻尼。这提高了高速时的稳定性,延长了电机寿命。
严格的制造公差。激光辅助卷绕(LATW- laser-assisted tape winding )工艺确保直接从生产开始进行高精度制造,减少了后加工的需要。
壁厚减小。通过在TPC套管中进行原位固结,优化了纤维铺设,使墙体更薄,同时保持强度,减少材料使用,提高空间效率。
环境可持续性。与热固性复合材料不同,热塑性加工消除了苛刻化学品的使用,使其成为一种更清洁和更可持续的替代品,具有低二氧化碳排放量,以及可在电机寿命结束时重复使用的材料。
室温处理。热塑性胶带焊接发生在局部加热点,使直接绕组到敏感部件,如永磁体,而不会有退磁的风险。
自定义材质属性。通过聚合物和纤维的正确组合,TPC允许控制套管厚度、导热性和CO2足迹,确保它们满足不同电机应用的精确要求。
可扩展性和自动化生产。LATW工艺实现了复合材料套筒的高速、自动化生产,确保了大批量制造中的一致性和成本效益。
Alformet的白皮书为行业的两个方面的工程师提供了资源——那些不熟悉复合材料的电机设计工程师,以及那些寻求了解电机要求的热塑性复合材料工程师。涵盖的关键主题包括:
转子和定子套管用热塑性复合材料与金属和热固性材料的比较; 设计注意事项,以最佳平衡性能设计、制造设计、成本设计和装配设计。 关于自动化和可扩展性如何使热塑性解决方案适用于工业生产的制造见解。------完-------

德国研究人员展示了纤维增强酚醛电机外壳和氧化铝填充环氧树脂二次成型定子集成冷却电路,以减轻重量,提高功率密度和效率。
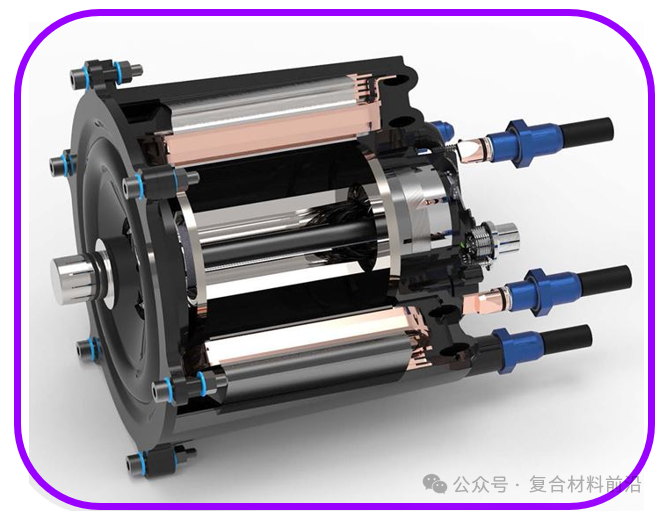
DEmiL项目电机的剖视图。电机的核心是一个定子,由12个单独的齿组成,这些齿使用扁平导线垂直缠绕。
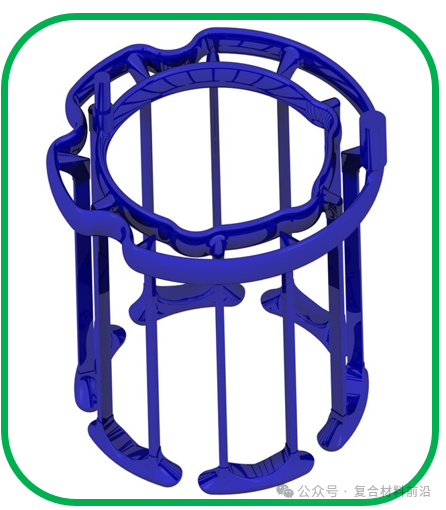
DEmiL项目电机定子中的冷却液回路
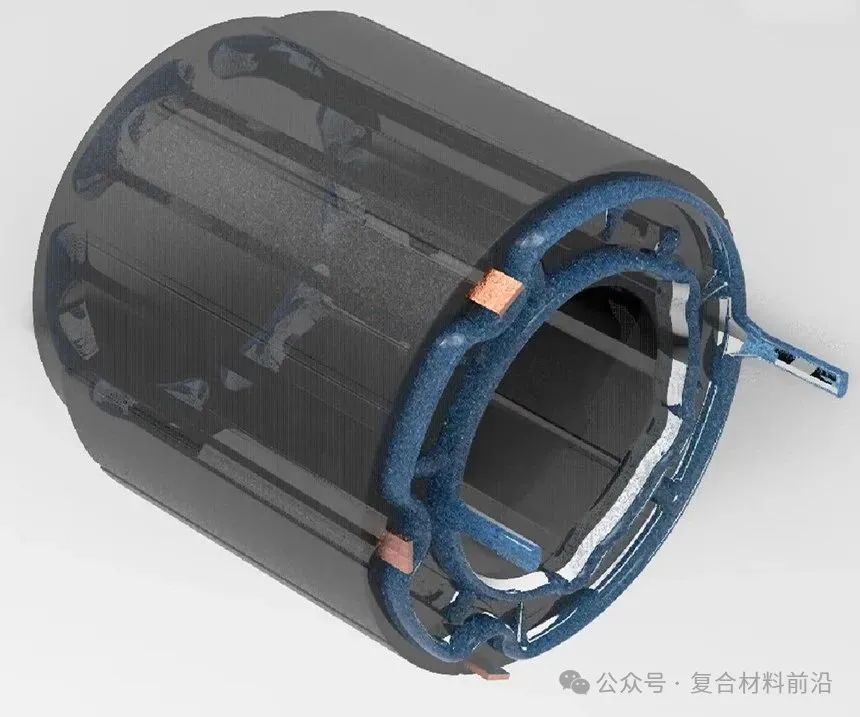
环氧树脂二次成型定子显示如何冷却电路(蓝色)集成,以更有效地散热,减轻重量
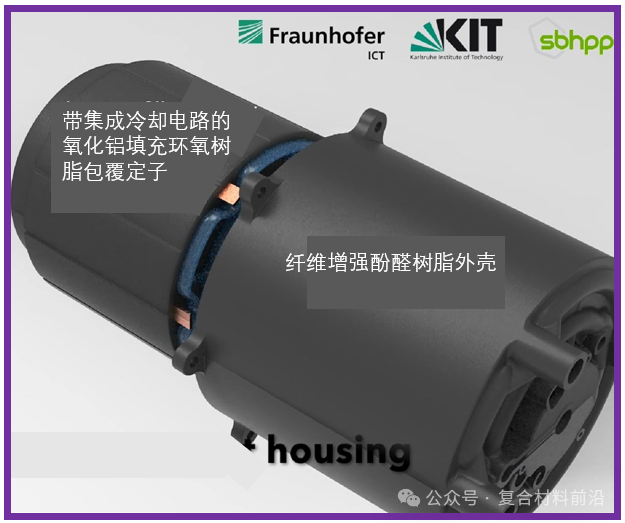
在DEmiL项目电动汽车电机中,采用增强热固性聚合物来减轻重量和提高效率
使电动汽车更轻还包括减少电机的重量。一种方法是用纤维增强聚合物材料来制造它。弗劳恩霍夫化学技术研究所ICT的研究人员正在与卡尔斯鲁厄技术研究所合作,开发一种新的冷却概念,使聚合物能够用作电机外壳材料。这并不是新冷却概念的唯一优点:与最新技术相比,它还显著提高了电机的功率密度和效率。
电动传动系的两个关键部件是电动机和蓄电池。在使用电动马达进行环保移动时,有三个问题起着特别重要的作用:高功率密度、紧凑的配置(与电动汽车紧密配合)和高效率。作为DEmiL项目的一部分,位于Pfinztal的Fraunhofer ICT的研究人员正在与卡尔斯鲁厄技术研究所的车辆系统技术研究所(FAST)和电气工程研究所(ETI)合作,开发一种将定子和转子直接冷却结合起来的新方法。Fraunhofer ICT研究员罗伯特·梅尔滕斯(Robert Maertens)说:“电动机由旋转转子和静态定子组成。定子包含电流流过的铜绕组,这是大部分电损耗发生的地方。我们新概念的新颖之处在于定子。”。
矩形扁线代替圆线
电动机的效率高达90%以上,这意味着大部分电能转化为机械能,剩下的10%左右的电能以热的形式损失。为防止电机过热,定子中的热量目前通过金属外壳传导至充满冷水的冷却套管。在这个项目中,研究小组用矩形扁平线代替了圆形线,这样可以更紧密地缠绕在定子中。这将为扁平导线绕组相位旁边的冷却通道创建更多空间。“在这种优化设计中,热损失可以通过定子内部的冷却通道耗散,无需将热通过金属外壳传输到外部冷却套管。事实上,在这种概念中,您不再需要冷却套管。它还提供了其他好处,包括较低的热惯性和较高的电机连续输出,” 梅尔滕斯说,并解释了新系统的一些优点。此外,新设计采用了转子冷却解决方案,还允许转子的热损失在电机内直接耗散。
通过在靠近产生热量的地方散热,项目合作伙伴能够用聚合物材料制造整个电机和外壳,从而获得进一步的优势。梅尔滕斯说:“聚合物外壳比铝外壳更轻,更容易生产。它们也适合复杂的几何结构,不需要后期处理,所以我们在总重量和成本上确实节省了一些。”。与金属相比,聚合物材料具有较低的热导率,可以取代目前作为导热体所需的金属。
项目合作伙伴选择使用其项目合作伙伴住友酚醛树脂(SBHPP)的纤维增强热固性塑料,该塑料具有耐高温性和高耐腐蚀性冷却剂性。与热塑性塑料不同,热固性塑料与化学品接触时不会膨胀。
适合大批量生产
聚合物外壳采用酚醛模塑料Vyncolit X7700在自动注射成型过程中生产。制造原型的周期目前为4分钟。定子本身采用导热环氧树脂模塑料(Sumikon EME-A730E)在传递模塑过程中二次成型。研究小组为电动机选择了一种设计和制造工艺,使其能够批量生产。
该团队已经完成了定子装配,并通过实验验证了冷却概念。梅尔滕斯总结了该项目的现状,他说:“根据模拟结果,我们使用电流在实际运行中产生的铜绕组中引入热量。我们发现,我们已经可以耗散超过80%的预期热损失。我们已经有了一些很有希望的方法来处理略低于20%的剩余热损失,例如通过优化冷却液流量。我们现在正处于组装转子的阶段,不久将能够在电气工程研究所的试验台上运行电机,并在实际运行中验证它。”。
------ 完 ------
原文,1. 《 Protecting EV motors more efficiently 》 2022.8.31
2. 《Alformet white paper examines untapped potential of TPC electric motor sleeves》 2025.2.20
3. 《Reducing heat in EV motors via fiber-reinforced thermoset housing and stator》 2019.2.18
杨超凡 2025.6.28
全部评论 (0)